Dental Office
Comments Off on Dental OfficeThe Challenge
A design build firm specializing in medical office buildouts and remodels was working on a new dental office in the same complex where HPS was installing a medical gas system for another client. The company’s owner happened to walk by our work area noticed our team’s work. Instantly recognizing our high quality and attention to detail, the owner approached the HPS project manager to ask if our team could also install medical gas piping for his new dental office nearby. The owner stated that it is difficult to find contractors who have the attention to detail he requires, as well as the certifications and knowledge to properly and safely install medical gas systems. He had been through an unpleasant experience in the past where a medical gas system was not properly installed and there was potential for litigation. He knew how critical it is that medical gas systems be installed properly and to code.
The Strategy
To install the medical gas system, HPS used CFOS (Cleaned for Oxygen Service) copper pipe and fittings, which are clean, bagged and hydro carbon free, to deliver oxygen to patients in a medical office.
In addition to stringent healthcare standards, this particular job had strict time constraints requiring flexibility from HPS. From an immediate mobilization and commencement of work, we needed to adapt our process in order to work in an occupied space with other construction trades, and the building firm owner was under a tight deadline to get the new dental office up and running. By adjusting our installation schedule to minimize disruptions for other occupants of the office building and keep noise levels at a minimum during early mornings and late nights, we finished the installation in just over a week.
Once complete, our installation underwent six rigorous tests including an initial system blowdown, primary pressure test, cross connection test, piping purge, 24 hour standing pressure testing, and third party analysis and verification to ensure that it met the current NFPA 99 Health Care Facilities Code — our system passed every test.
The Result
It is a testament to our commitment to excellence on every project that a client so dedicated to quality installations took notice of our work and approached us with an inquiry. The firm was pleased with our open communication and willingness to adapt to their schedule, which led to continued collaboration on several projects since the initial installation.
Contact High Purity Systems
Have a question about a piping challenge? Want to discuss an upcoming project? Let’s talk.
Aluminum Welding
Leave a CommentThe Challenge
Recently, a leading designer and manufacturer for the military and aerospace industries approached HPS to request our fabrication and aluminum welding expertise in helping weld their aluminum cooling flanges.
Our client, a globally recognized pioneer in laser technology and electro-optical sensors, had state-of-the-art laser and electro-optical systems that required large amounts of cooling. They provided us with a custom machined 6061 aluminum cooling flange with 37° aluminum VCR flare fittings, and asked us to weld them together.
The Strategy
With over 30 years specializing in specialty welding, HPS knew the best way to tackle the job. Referring to a customer-supplied drawing, HPS used precipitation hardened alloy 6061 aluminum and ER5356 filler to weld the fitting to the client’s exact specifications and all associated standards.
When welding aluminum, helium leak testing can be an arduous challenge. If not done correctly, aluminum’s porous nature can lead to warpage and damage the fittings. To combat these concerns, HPS performed in-process tests and QA/QC inspections throughout the procedure including: a helium leak check, argon pressure test, and flatness check / horizontal plane to ensure the fitting met all of the client’s expectations.
The part was only 3” x 4” overall, with flange face flatness held within an extremely tight tolerance of 0.002”. The highly critical dimensional tolerances were achieved through the use of extremely talented craftsmen, and the proper type of welding equipment, which is recognized for its superior arc-shaping capabilities. Upon final completion, the flange received a full Helium Leak check test. HPS turned this special project around for our client within one week.
The Result
Operating in the aerospace industry, precision is critical. Based on their previous work with HPS and knowledge of our broad range of custom welding capabilities, the customer trusted us to carefully weld the fittings, minimize distortion, and lower the porosity level to a leak-tight fit.
HPS’ industry expertise and strong collaboration with the client led to a quick and precise execution of the project. With our extensive track record and expertise in a wide variety of techniques, the client knew they were in good hands. The customer called and High Purity Systems delivered!
Interested in a collaboration with High Purity Systems? Contact us now.
Contact High Purity Systems
Have a question about a piping challenge? Want to discuss an upcoming project? Let’s talk.
Gas Outlet Upgrades
Leave a CommentThe Challenge
At HPS, we pride ourselves on our experience in meeting the strict standards of the healthcare industry. Recently, for instance, a Northern Virginia-based health care center needed help fixing an oxygen (O2) leak in their facility. Having heard of our experience on similar projects, they turned to us for a quick response.
The Strategy
To solve the problem, our team was asked to upgrade 12 oxygen wall outlets, complete with new latch valves and O-rings. We jumped right in and began planning how to adapt the new HPS-provided Amico wall outlets to fit within the customer’s specifications and existing system.
Because we were working in the facility while it was still operating, our team had to be flexible. We adapted to the customer’s schedule to install the 12 CFOS Medical Gas copper outlet valves in a four-hour period, minimizing any inconvenience to the staff and residents. After the installation was complete, our on-site team performed an in-service test to confirm it met stringent NFPA 99 Medical Gas specifications.
The Result
Our team turned this project around in just one day, allowing the health facility to return to its regularly scheduled operations almost immediately. We were proud to be trusted not only with a time-sensitive project, but also one that demanded the utmost precision and purity.
In addition to being an NFPA 99 Medical Gas Certified Installation contractor, HPS also has the capabilities to adhere to ASME Section IX brazing and welding standards. To learn more about our previous work in the healthcare industry, or to discuss your next project, contact us today.
Contact High Purity Systems
Have a question about a piping challenge? Want to discuss an upcoming project? Let’s talk.
Hastelloy® Pipe Welding
Leave a CommentThe Challenge
High Purity Systems’ (HPS) fabrication services, clean system installations, welding capabilities, and extensive industry knowledge recently won our team a fabrication and installation project with a leading water and wastewater management service provider.
The customer, a general contractor working with a water and wastewater treatment plant, needed to install Hastelloy® piping for its sulfuric acid and sodium hydroxide systems. Neither the contractor nor the end user had much experience with this material, whose exotic nature posed huge risks of welding failures and added costs. Unable to find anyone capable of welding Hastelloy® pipe, the customer turned to the welding experts at HPS.
The Strategy
Not only did HPS have the experience and qualifications to work with this rare piping material, but we were able to adjust our project schedule to fit the customer’s needs, as well as fabricate much of the work offsite to minimize congestion on the project. We visited the customer’s site to detail the piping, then fabricated as much as possible in our Manassas, Virginia pipe fabrication shop before returning to the site for installation.
Using pipe cutting equipment and TIG welding machines, HPS installed 200 linear feet of the 0.75” Hastelloy® 40 pipe, and when complete our team pressure tested the entire installation to ensure that it met American Society of Mechanical Engineers (ASME) B31.3 power piping standards.
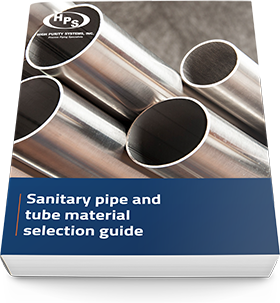
Sanitary pipe and tube material selection guide
See how matching materials to processes boosts performance and increases safety in your operations.
As a side note, the end user was challenged with numerous obstacles on their end before HPS even entered the picture – slow turnaround for submittals and RFI’s combined with long lead times for parts and materials – which ended up delaying the project schedule from an original duration of eight weeks to an extended five-month timeline. HPS was able to provide flexibility for our customer, and through proactive dialogue and communication with the contractor, the designer, and the end user, we were able to execute the project in the most timely and efficient way possible.
The Result
HPS’ previous experience and knowledge of Hastelloy® added value to the project and ultimately convinced the contractor to trust us with the job. After the successful installation, the contractor continued utilizing our technical expertise to help educate their team and the end user. We were proud that this job led to not just one, but many happy customers!
Contact High Purity Systems
Have a question about a piping challenge? Want to discuss an upcoming project? Let’s talk.
Chromatography Skid Modifications
Leave a CommentThe Challenge
In recent years, High Purity Systems (HPS) has seen a big push for equipment upgrades requiring expertise in biopharmaceutical orbital welding. As an experienced contractor and trusted partner with many life-science laboratories, we’ve been approached time and time again to help companies make these critical system updates.
Recently, a customer in this industry came to us with a time sensitive job that could not afford any downtime; one of their chromatography skids was in desperate need of revitalization. Functioning at suboptimal performance, this prevented the customer from getting accurate measurements on the ratios of their mixtures — a serious issue when pharmaceuticals are involved, as even minute discrepancies in the parts-per-million range can be catastrophic to an entire product batch. Because we had delivered systems to them in the past, this client knew that HPS could get the job done efficiently and on time.
And having heard specifically of our team’s previous experience with biopharmaceutical orbital welding and skid work of all sizes and functionalities, the customer knew we could manage the heavy workload and sensitive timeline.
The Strategy
HPS was tasked with completing a job that should have taken two and half weeks in just a one-week period—but this was nothing we couldn’t handle. Starting with the bottom of the skid, our field service crew relocated a 2-inch drain valve to the opposite side of the main valve. After we cut off the drain valve, we faced the remaining tube for welding, cleaned it, and manual TIG welded a new piece of 316L stainless steel tube in its place.
We then faced, cleaned, and welded the old drain valve into its new home and piped out an automated steam trap from the new drain valve location. We also needed to orbital weld a pressure controller into a line in the middle of the skid, along with two new sanitary ferrules. In the last part of the steam piping orbital welding phase, we cut in and installed a new temperature sensor on the skid.
All of the welds our team made were spot passivated, inspected, and documented to meet the FDA’s requirements for validated systems, as well as ASME BPE specifications. To make the documentation official, the inspection was borescoped and recorded by a third-party quality control team checking our work.
The Result
With nothing but a small list of instructions and a few photographs for reference from the customer, the HPS foreman and crew knew how to get the job done. Our team is proud to have earned this level of trust with our customers — the kind that is only built after years of delivering high-quality, reliable systems.
This customer trusted our team because they knew we were consistently safe in our processes and have had years of practical experience fabricating and installing bioprocessing equipment, sanitary pipe, and sanitary piping systems. With our qualified, detail-oriented craftsmen and meticulous, knowledgeable office staff, HPS is proud to be an industry-leading high-purity mechanical contractor specializing in biopharmaceutical orbital welding.
To learn more about our past work or discuss your next project, reach out today.
Contact High Purity Systems
Have a question about a piping challenge? Want to discuss an upcoming project? Let’s talk.
UHP Valve Panel
Leave a CommentThe Challenge
At HPS, we pride ourselves on our diverse fabrication capabilities, which allow us to quickly transition from one job to the next. For instance, one of our recent projects came about when we overheard a client express frustration about an original equipment manufacturer (OEM). The customer, a microelectronics company, was dissatisfied with the OEM’s hefty price tag and long lead time for a valve manifold panel (VMP).
The existing VMP, located in our customer’s gas delivery room, needed to be discarded after one of the gas boxes had become contaminated. Stuck without any replacement panels and scrambling for a solution, the customer could not afford to wait the 12-14 weeks it would take for the OEM’s fabrication to arrive from France. Every hour that our client’s panel was nonoperational was costing them time and money.
The Solution
Understanding the urgency of the situation, HPS proposed to fabricate replacements for all of the panels that received gas from the contaminated line. Our team suggested a duplicate panel with the exact same inlet and outlet connections and dimensions as those made by the OEM.
We suggested using alternate valves that offered equal quality and service, despite coming from a different manufacturer. To demonstrate this equivalency, HPS supplied the customer with the cut sheets and specifications for all valves, regulators, venturis, and pressure transducers — all of which they approved.
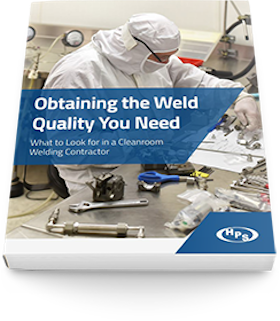
Obtaining the weld quality you need
Learn about the skills and resources necessary for successful cleanroom welding.
Utilizing an automatic GTAW orbital welding machine, we fabricated a 12 in. x 18 in. stainless steel panel with an electropolished surface finish, complete with the associated components, fittings, and tubing. Our Ultra High Purity (UHP) welds were to semiconductor standards and held tolerances within 0.030 in. of the existing panel dimensions.
The Result
In less than five weeks, HPS was able to duplicate the panel in our Class 100 clean room and provide an OEM replicated solution. The customer was so pleased with the results that they immediately ordered two more panels.
To learn more about HPS’s capabilities or to discuss how we can help you with your next project, contact us today.
Contact High Purity Systems
Have a question about a piping challenge? Want to discuss an upcoming project? Let’s talk.
Water Feature Piping
Leave a CommentThe Opportunity
Few men and women have given more to our country than the individuals who have returned home disabled after their service. In late 2013, High Purity Systems was honored to be awarded the stainless steel pool and fountain piping for the construction of the American Veterans Disabled for Life Memorial (AVDLM) to recognize these heroic service members.
The memorial stands south of the Botanical Gardens and adjacent to the US Capitol and the House of Representative office building, and interestingly — directly on top of the 395 highway tunnel in the District of Columbia. AVDLM’s design includes etched glass panels, stone walls, bronze statues, and a placid reflecting pool that transitions into a star-shaped pool with an eternally bubbling ceremonial flame.
Many memorials have special water features, such as fountains or pools. These water features require underground specialty stainless steel plumbing that needs to last for many, many years. At AVDLM there is no typical vertical spraying fountain. The star pool is a flowing water pool with a water fall feature over the edges of the star. The other pool has very calm, glass-like water which creates the reflecting pool feature. Below the surface of the calm reflection and the flame, 140 gallons of water per minute are flowing to filter, recirculate, and maintain the proper water levels in each of the two pools. Therefore, all of HPS’ piping is hidden under the pool area and covered with dirt, concrete, granite and etched glass walls.
The Strategy
In order for the concrete to be poured on time, allowing the stone masons and landscapers to get to work, our team had to fast-track the piping construction. We detailed the piping in phases and utilized our pipe fabrication shop in Northern Virginia to weld the stainless pipe using the Miller Regulated Metal Deposition (RMD) process. Our off-site fabrication supported our on-site crew of five team members that assembled the fabricated piping spools and completed the final field welds using a TIG process.
The memorial required fill piping, filtration piping, as well as recirculation suction and discharge piping, ranging from 1-1/2” Sch40 to 12” Sch10 stainless steel. These piping systems connected the equipment from inside the pump house to the basin and trough of the star pool and the upper trough, lower trough of the reflecting pool as well as feeding the reflecting pool itself.
Because the job had to be completed in phases (or multiple layers in this case), HPS would alternate installing a layer of pipe and then switch places with another trade to pack dirt or run electrical services. HPS would then return to the site to repeat the process. Being a reflecting pool with thousands of square feet of surface area, fractions of an inch in elevation were critical to the stone work that would cover our piping feeding the pool. Once the underground piping was complete, we focused our efforts on the pump house, where we installed all of the main piping and headers, as well as the finish items such as pressure gauges, temperature sensors, and regulators.
Since this fountain is in Washington DC, where winters include frost and freezing temperatures, all piping had to be installed with a slope back to the equipment vault to allow for complete draining and winterization.
When building an underground piping system to service a beautiful memorial such as AVDLM, it is critical to deliver the best product possible. Every HPS weld was made to the highest standards under ASME B31.3 codes with top quality materials purchased under the Buy American Act.
The Result
HPS was involved in the memorial’s construction for approximately six months, fabricating and installing the pipe, performing multiple stages of hydrostatic pressure testing, and delivered proudly on time.
Once the memorial was completed in October 2014, there was a dedication ceremony for Armed Forces Officers, enlisted service members, and political officials. Many of the behind the scenes individuals and disabled veterans — some of whom were memorialized on the etched glass panels — gave heartfelt speeches about their country, the memorial, and the contractors who built it.
High Purity Systems was honored to be part of the team that built the American Veterans Disabled for Life Memorial, which recognizes and honors those who live every day with the disabilities they incurred while serving our country.
Contact High Purity Systems
Have a question about a piping challenge? Want to discuss an upcoming project? Let’s talk.
Pure Water System
Leave a CommentThe Challenge
HPS is proud to provide high-quality piping systems for some of the most innovative, successful companies across industries. One of our recent customers — a Maryland-based biopharmaceutical and life science company — was working on a facility expansion and needed to build a Reverse Osmosis/Deionized (RODI) water system to deliver purified water. Accustomed to working on detailed, complex projects, we at HPS knew we would be the right contractor for the job.
We teamed up with our equipment vendor to put together a presentation demonstrating our understanding of the customer’s specific needs and also built a résumé of past projects involving the installation of similar critical piping systems. After a thorough and competitive bid comparison process, our proposal was accepted, and our project team immediately began scheduling and organizing all necessary resources.
The Strategy
With a team of just two men, we installed over 700 feet of 2-inch 316L stainless steel piping. Using orbital welding technology, our team loop routed the tubing throughout the ceilings and clean space areas with multiple single- and double-type ZDL (Zero Dead Leg Valve) POU drops feeding sinks, washers, and autoclave equipment. After finishing the installation, our third party Certified Weld Inspector (CWI) used a borescope to ensure our welds were up to BPE standards.
We also installed a polypropylene (PP) soft water piping system with a loop originating and concluding in the mechanical water room using IR fusion equipment to butt weld the PP system together. Our team added and interconnected a custom fabricated pure water generation skid, which included a storage tank, pretreatment and hot water sanitization features, carbon filters, reverse osmosis (RO) capabilities, pumps, a heat exchanger, and a bacteria ultra violet (UV) unit.
Not only did our team need to complete this highly complex piping system on a strict timetable, we also utilized BIM modeling to coordinate layout with other trade contractors working simultaneously on-site. Based on past projects in similar environments, our field staff understood the importance of being self-sufficient in this type of atmosphere, allowing the Construction Manager (CM) to focus his attention on other teams that required assistance and preventing potential obstacles.
The Result
In just eight short weeks, our team completed the Water for Pharmaceutical Use (WPU) piping system — a critical part of a complex building renovation — as well as a fully validated BPE Turnover Package for final customer validation. The CM was very impressed with our ability to work independently and efficiently on such a busy job site while turning the project around 100% on time, with no complications.
To learn more about HPS’s experience working on complex piping systems for various applications or to discuss how we can assist you with your next project, reach out to us today.
Contact High Purity Systems
Have a question about a piping challenge? Want to discuss an upcoming project? Let’s talk.
Natural Gas Piping
Comments Off on Natural Gas PipingThe Challenge
In 2015, one of our valued oil and gas customers reached out to our High Purity Systems team with a problem.
As a supplier of natural gas in the Washington, DC metro area, the company was responsible for maintaining thousands of miles of piping infrastructure. Accountable for so much piping, the customer had to carefully adhere to public safety standards and conduct continuous upgrades.
While performing routine maintenance on a generator/compressor, they discovered that the equipment’s outer piping blocked access to the compression chambers. This is not an uncommon issue, but rather a simple challenge of accessibility. When dealing with such large equipment — the compressor was as big as two shipping containers stacked on top of one another — easy access is a must.
The Strategy
The customer contacted HPS thanks to a long history of projects we had previously completed for them. They knew that with fast and experienced welders, HPS could get the system back on line quickly. HPS safely and efficiently cut out the 8” pipe so we could continue working on the compressor.
After talking to the client, our team determined that we should install two flanges at the site of the cut-out to facilitate any future maintenance. We ordered two 8” 300# carbon-steel flanges to be shipped to the customer’s site. When HPS’ weld crew arrived on site, they completed a routine assessment of the work area and immediately made safety improvements. After covering holes in the floor and securing the ladder, the crew began the flange installation.
The crew prepped the welded joints, and efficiently demobilized. All in perfect time for our third-party nondestructive testing (NDT) expert to x-ray the joints and turn them over to the customer.
The Result
The story does not end there: based on the quality and speed of HPS’ work, our customer’s equipment vendor commissioned HPS to make additional stick welds for the same compressor. The vendor needed plate-steel welded to the bottom of the compressor supports in order to shim the intricate equipment. The HPS fabrication shop created, cleaned, and delivered plates the next day.
The result of the initial gas project was not just one, but two happy customers. Want to join them? Contact us today.
Contact High Purity Systems
Have a question about a piping challenge? Want to discuss an upcoming project? Let’s talk.
Ammonia and Silane
Leave a CommentThe Challenge
High Purity Systems (HPS) is a clean piping system installation and fabrication service provider for the semiconductor, aerospace, and bio-pharmaceutical industries, and our team recently showcased its diverse capabilities when a large microelectronics company approached our staff for help.
The customer — a global fiber optics, motion control, light analysis, and optomechanics product manufacturer — needed to relocate its existing ammonia (NH3) and silane (SiH4) gas cabinets and the associated ductwork and piping. They turned to our team, with years of experience in field service and project management experience, to guide this multi-step gas system installation project from start to finish.
The Strategy
We differentiate ourselves by having a thorough understanding of our customer’s specific facility protocols, as well as the client’s end goals and project deadline. Our on-site team knew the right questions to ask to better understand the client’s daily operations and adapt our work process to fit their needs accordingly.
Upon having a clear understanding of the customer’s work environment, we disconnected the existing gas cabinets and removed the ductwork and associated piping. We then relocated the cabinets to the desired location and added new silane, ammonia, compressed air, nitrogen, and oxygen lines, as well as ductwork for the exhaust.
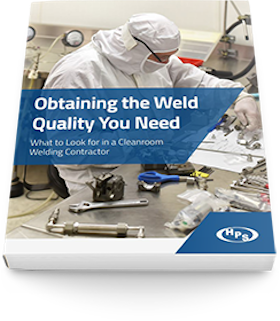
Obtaining the weld quality you need
Learn about the skills and resources necessary for successful cleanroom welding.
Using an orbital welding process, our team installed 316L stainless steel ammonia and silane lines with coaxial tubing to create a double contained system. VCR and compression fittings secured the 15Ra, 1/4″ x 1/2” coaxial gas lines.
Upon completion of the installation, a pressure test was performed on both the inner 1/4” process line and the outer 1/2” containment line, as well as analytical testing to confirm purity. The finished product, which met the international SEMI standards for cleanroom safety and cleanliness, was turned over to the customer in three weeks.
The Result
This multi-step gas cabinet relocation and installation demonstrated that in addition to our work in smaller research and development labs, HPS also executes projects in larger semiconductor manufacturing plants. This project demanded HPS’ expertise with ultra-high purity cleanroom piping systems as well as double containment coaxial systems for hazardous materials.
The customer chose our team for our strong industry reputation and extensive resume, and we provided them with competitive pricing and flexible start and completion dates to meet their manufacturing schedule.
Think we can work together to solve a similar problem in your facility? Contact us now.
Contact High Purity Systems
Have a question about a piping challenge? Want to discuss an upcoming project? Let’s talk.