Sanitary Brewery Piping Installation
Leave a CommentThe Challenge
HPS has been a leader in sanitary process piping systems for over 30 years, and one of our favorite types of customers is beverage production plants. Recently, an award-winning microbrewery needed a mechanical contractor to modify and add transfer lines to their production facility.
The job was multifaceted, requiring uphill and downhill stainless transfer lines, CIP system piping, adding sanitary ferrules for existing piping, equipment and piping racks, structural steel legs for an outdoor piece of equipment, and piping insulation. The customer chose HPS for this complex project after another local Brewmaster referred us for our diverse mechanical capabilities, quick response time, and knowledge of sanitary brewery piping systems.
The Strategy
Our team knew it was important to limit any impact on the brewery’s production, so we decided to detail and prefabricate many of the modifications off-site in our piping fabrication shop. Using an orbital TIG welding machine, our certified ASME Section IX welders fabricated the piping out of 304 and 316L stainless steel to meet 3A sanitary standards for the food and beverage industry.
We completed the final installation on a day the bottling crew was not working. Off-site fabrication of the sanitary brewery piping meant we could come to the facility and quickly incorporate the modifications with minimal disruption to its daily operations.
The Result
Our team was able to complete the project in two weeks, and exceed the customer’s expectations in the process. In fact, on our last day of work, the owner asked if we also did steam piping and glycol piping – the answer was a resounding yes! We were proud to be selected as a trusted partner in the tight-knit brewing community and we look forward to many more projects to come.
HPS not only performs sanitary brewery piping installation, but also fabricates carbon steel steam lines and glycol systems, copper piping, PVC plastic, non-process systems, custom parts such as sanitary hoses, and tank rigging services. As your brewing, distilling, or winemaking facilities grow and evolve, remember that quality and doing it right the first time are the keys to reducing costs and downtime. Whether on-site installations, off-site custom fabrications or general facility maintenance, we are here to help!
To talk through a challenge at your facility, contact our team.
Contact High Purity Systems
Have a question about a piping challenge? Want to discuss an upcoming project? Let’s talk.
Sanitary Dip Tubes
Leave a CommentThe Challenge
Having heard of our reputation as a leading sanitary equipment and parts manufacturer, a global healthcare company approached High Purity Systems (HPS) to see if we could apply our custom metal fabrication expertise to their latest project. The company, which researches and develops medicines, vaccines, and consumer healthcare products, asked HPS for help building sanitary dip tubes for a small reaction vessel.
Need Sanitary Dip Tubes? Reach out to Our Sales Team Today
In chemistry, reaction vessels are the spaces used to contain reactants — the substances that change form in a chemical reaction. As a research-led healthcare company, the client uses these vessels regularly for biopharmaceutical testing and development. They turned to HPS to fabricate dip tubes in accordance with the strict American Society of Mechanical Engineers’ Bio Processing Equipment (ASME-BPE) hygienic standards.
The Strategy
HPS performed the fabrication and installation in just three weeks by welding 0.75” sanitary Grade 316L stainless steel tubing with an orbital welding system and finishing it with 20Ra electro-polish surface finish. The finished dip tube underwent one final inspection for dimensional accuracy and was verified with a profilometer to ensure it met our customer’s requirements.
The Result
The customer chose High Purity Systems based on previous work we had done together, noting they were impressed not only with the quality of our work but also with our BPE documentation of the process. After we completed the dip tube project, the client again expressed satisfaction with our communication in determining requirements, as well as our ongoing exchanges throughout the fabrication.
Our industry knowledge and continued collaboration with the client led to a successful installation that met the strict AMSE-BPE requirements and elicited positive customer feedback. Through our proven expertise on custom projects, adherence to strict specifications, and cooperation with our customer, HPS once again exceeded client expectations.
Need Sanitary Dip Tubes? Reach out to Our Sales Team Today
Contact High Purity Systems
Have a question about a piping challenge? Want to discuss an upcoming project? Let’s talk.
Biowaste Drain
Comments Off on Biowaste DrainThe Challenge
A biopharmaceutical manufacturer contacted High Purity Systems (HPS) to request a modification to its stainless steel Biowaste Drain system. The project entailed modifying the existing stainless steel line during a scheduled plant shutdown.
The Strategy
The customer chose HPS for our stainless steel pipe welding expertise, competitive pricing, and, most importantly, our ability to perform in critical shutdown conditions. The client was impressed by our safety record on past projects, attention to detail, and ability to understand the scope of work within required deadlines.
The client had confidence that HPS would work to get the facility back up and running as quickly and safely as possible. With proper planning and allocating the right resources, the HPS team ensured that the client faced minimal risk during the shutdown.
HPS first fabricated and replaced an existing 4” stainless steel biowaste drain system. While working to modify the drain system, our team also encountered five other related tasks, all of which needed to be completed by the end of the client’s one-week plant shutdown period. With proactive planning and careful organization, we were able to complete each of the time-sensitive tasks within the one-week timeframe, as well as perform thorough in-service testing of the drain system.
The Result
In the end, we succeeded in completing the drain bypass while exceeding the customer’s expectations for the strict shutdown schedule. For our work with this biopharmaceutical manufacturer during a critical plant shutdown, our client even awarded the High Purity Systems crew a Safety Recognition Medal! We are truly blessed to work for clients who share our safety culture that every accident is preventable.
To discuss a potential project in your facility, contact our team today.
Contact High Purity Systems
Have a question about a piping challenge? Want to discuss an upcoming project? Let’s talk.
RODI Water
Leave a CommentThe Challenge
A few years ago, an experienced mechanical contractor approached the HPS team about a special piping project. This company needed an experienced piping contractor who could handle the detailed requirements associated with installing a Reverse Osmosis/Deionized (RODI) water system in a life science lab facility.
Having already worked with this mechanical contractor on a previous project to quickly and properly install a similar system at a university, they knew they could trust us with the job.
The Strategy
Life science facilities can demand a lot of water; and this project consisted of a RODI loop and numerous drops on two different levels of two separate buildings. Our team needed to connect the two buildings to form one massive loop supplying all the lab stations. Because of its naturally smooth inner surface finish, limited degradation when exposed to RODI water, and being a cost competitive material and installation process, natural polypropylene was chosen as the loop material.
The HPS site team had to work alongside many different trades in crowded areas to complete the loop. The material specifications did not allow mechanical unions to be used within the piping system, which meant HPS had to perform field welds in difficult aerial positions with a Georg Fischer butt fusion welding machine. The result was a contiguous, leak-free system in the ceilings and walls.
Each plastic fusion weld received a verification label in accordance with FDA documentation requirements for weld tracking and, upon completion, the system was flushed and pressure tested with DI water in compliance with customer specifications.
The Result
This specialty installation is one of the largest RODI systems HPS has tackled to date. A six month job with three more months of additional scope, the finished project was a beautiful and fully functional RODI loop piping system. The owner and the GC were pleased with the result, and the mechanical contractor continues to reach out to us to work on similar projects.
Interested in collaborating with High Purity Systems? Start the conversation here.
Contact High Purity Systems
Have a question about a piping challenge? Want to discuss an upcoming project? Let’s talk.
Control Panels
Leave a CommentThe Challenge
Few industries are as demanding and exacting as aerospace, but High Purity Systems has proven itself to be a reliable, detail-oriented partner for critical ground support operations during a number of projects over the years. Another aerospace company recently approached us to provide four custom control panels for pressure and instrumentation at one of its ground support facilities.
The panels needed to recirculate and purge a critical fluid volume within a specifically designed configuration that would control and monitor volume, pressure, and flow rate. The customer sought out HPS because its team knew of our previous aerospace experience and our reputation for turning around quality work under tight deadlines.
The Strategy
To begin the custom fabrication, the customer provided HPS with piping schematics and specifications, which called for our team to create a custom 3D layout to meet the customer’s requirements. Once the layout was approved, HPS utilized our tube bending and flaring equipment to fabricate the control panels out of customer-supplied 6061 aluminum mounting plates and 316L stainless steel tubing and fittings.
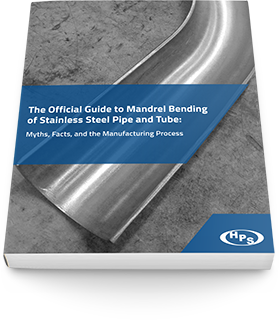
The official guide to mandrel bending
Separate facts from myths and save up to 50% on project costs compared to cutting and welding.
In order to match the facility’s existing panels, we applied a Tiger Drylac powder coat finish to the aluminum pieces before installing them with a combination of compression fittings, O-ring boss fittings, JIS 37˚ flare fittings and flare adapters, and MS and AN fittings.
After completing the panels, our fabrication team pressure tested the panels with National Institute of Standards and Technology (NIST) certified gauges and torque fittings to ensure compliance with customer specifications.
The Result
The final products were a 3’x4’ recirculation pump purge panel, a 3’x4’ differential pressure purge panel, and a set of two 6’x4’ pressure and instrumentation panels. Our fabrication team turned this project around just four weeks after receiving the materials from the customer. The project demonstrated our ability to manage complex layouts and deliver high-quality results on a strict timeline.
Are you considering a complex project and want to consult with us? Contact High Purity Systems now.
Contact High Purity Systems
Have a question about a piping challenge? Want to discuss an upcoming project? Let’s talk.
Overflow Valve
Comments Off on Overflow ValveThe Challenge
One of our industrial customers needed to install a valve and vent pipe on an underground steam drain system.
Seems easy enough, right? Not exactly.
While High Purity Systems (HPS) was performing the overflow valve installation, we discovered a significant challenge with the drain pipe: the underground pipe was a different material than what was previously specified. HPS conquered this challenge by drawing from our industry expertise and history of problem solving with unique projects.
Thanks to our long standing relationship, the customer had confidence in our team’s ability to complete the project and overcome the identified obstacles.
The Strategy
At HPS, safety is our number one priority — regardless of whether we are in the trenches or preparing to work within them. Once the client selected us for the job, HPS began planning for the safety and execution of an exciting new project.
First, we began with the excavation and exposure of the underground piping system. By utilizing an extending forklift and mechanical couplings for cross-material linking, we broke ground and prepared to install the drain pipe material.
It was only after excavating that we discovered the piping material was cast iron, not carbon steel as we had originally thought; welding the valve to the pipe using this material was not feasible. We needed to find an alternative approach to the project while still staying within our client’s requested timeline.
The Result
High Purity Systems quickly identified a solution and, in the end, was able to meet specifications while completing installation just a week later. The end result was 4” piping with ¼” tolerances. Not only did HPS complete the renewed drain piping system, but we also did it swiftly to solve a problem that could have caused major delays for our customer.
Can HPS become a problem solving partner for your business? Let’s connect.
Contact High Purity Systems
Have a question about a piping challenge? Want to discuss an upcoming project? Let’s talk.
Argon Lab Gas Piping
Leave a CommentThe Challenge
One High Purity Systems (HPS) customer, a photonics developer focused on the industrial, scientific, and medical industries, came to our team for help with their argon delivery system. The company, which works with energy systems such as ultra-violet (UV) and infrared (IR) light, needed to expand from an individual bottle setup to a bulk gas delivery system.
The Strategy
Using an orbital welding process, the HPS site team installed ½” stainless steel 316L 15Ra electropolished (EP) tubing from the photonics lab area to the outdoor gas storage pad. The argon piping system was orbital welded to minimize any risk of leaks throughout the building.
A gas panel was also relocated during this project. The entire argon system was installed, tested, and ready for service in just three weeks with minimal impact to our customer’s daily operations.
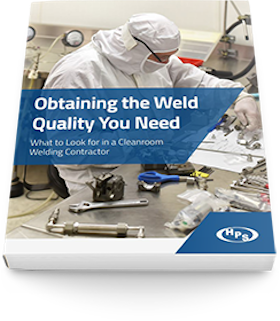
Obtaining the weld quality you need
Learn about the skills and resources necessary for successful cleanroom welding.
The Result
The client chose HPS for this job based on a recommendation from a vendor who had previously seen our quality craftsmanship at other facilities and knew that we are skilled at clean gas system installations. This project shows our industry-leading knowledge of proper and efficient installations for semiconductor grade high purity piping systems.
The customer was impressed with a job well done, and very happy they took the vendor’s advice to call us!
You can call us too—do it here.
Contact High Purity Systems
Have a question about a piping challenge? Want to discuss an upcoming project? Let’s talk.