The Challenge
Few industries are as demanding and exacting as aerospace, but High Purity Systems has proven itself to be a reliable, detail-oriented partner for critical ground support operations during a number of projects over the years. Another aerospace company recently approached us to provide four custom control panels for pressure and instrumentation at one of its ground support facilities.
The panels needed to recirculate and purge a critical fluid volume within a specifically designed configuration that would control and monitor volume, pressure, and flow rate. The customer sought out HPS because its team knew of our previous aerospace experience and our reputation for turning around quality work under tight deadlines.
The Strategy
To begin the custom fabrication, the customer provided HPS with piping schematics and specifications, which called for our team to create a custom 3D layout to meet the customer’s requirements. Once the layout was approved, HPS utilized our tube bending and flaring equipment to fabricate the control panels out of customer-supplied 6061 aluminum mounting plates and 316L stainless steel tubing and fittings.
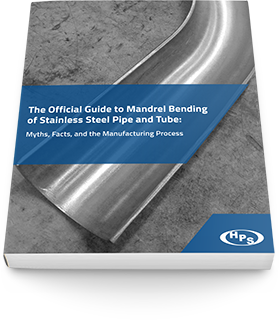
The official guide to mandrel bending
Separate facts from myths and save up to 50% on project costs compared to cutting and welding.
In order to match the facility’s existing panels, we applied a Tiger Drylac powder coat finish to the aluminum pieces before installing them with a combination of compression fittings, O-ring boss fittings, JIS 37˚ flare fittings and flare adapters, and MS and AN fittings.
After completing the panels, our fabrication team pressure tested the panels with National Institute of Standards and Technology (NIST) certified gauges and torque fittings to ensure compliance with customer specifications.
The Result
The final products were a 3’x4’ recirculation pump purge panel, a 3’x4’ differential pressure purge panel, and a set of two 6’x4’ pressure and instrumentation panels. Our fabrication team turned this project around just four weeks after receiving the materials from the customer. The project demonstrated our ability to manage complex layouts and deliver high-quality results on a strict timeline.
Are you considering a complex project and want to consult with us? Contact High Purity Systems now.
Contact High Purity Systems
Have a question about a piping challenge? Want to discuss an upcoming project? Let’s talk.