The Challenge
One High Purity Systems (HPS) customer, a photonics developer focused on the industrial, scientific, and medical industries, came to our team for help with their argon delivery system. The company, which works with energy systems such as ultra-violet (UV) and infrared (IR) light, needed to expand from an individual bottle setup to a bulk gas delivery system.
The Strategy
Using an orbital welding process, the HPS site team installed ½” stainless steel 316L 15Ra electropolished (EP) tubing from the photonics lab area to the outdoor gas storage pad. The argon piping system was orbital welded to minimize any risk of leaks throughout the building.
A gas panel was also relocated during this project. The entire argon system was installed, tested, and ready for service in just three weeks with minimal impact to our customer’s daily operations.
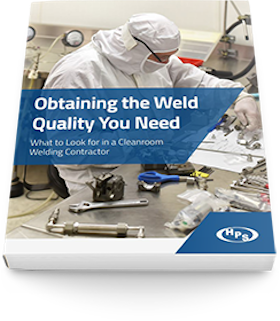
Obtaining the weld quality you need
Learn about the skills and resources necessary for successful cleanroom welding.
The Result
The client chose HPS for this job based on a recommendation from a vendor who had previously seen our quality craftsmanship at other facilities and knew that we are skilled at clean gas system installations. This project shows our industry-leading knowledge of proper and efficient installations for semiconductor grade high purity piping systems.
The customer was impressed with a job well done, and very happy they took the vendor’s advice to call us!
You can call us too—do it here.
Contact High Purity Systems
Have a question about a piping challenge? Want to discuss an upcoming project? Let’s talk.