Launch Pad Piping Install
Leave a CommentThe Opportunity
Our team was excited to have an out-of-this-world opportunity to build ground support infrastructure at a NASA rocket launch pad, located at Wallops Island, VA, for a new liquid fueling facility (LFF) to support an unmanned rocket resupply mission to the International Space Station (ISS).
High Purity Systems (HPS) has over 30 years of experience with a broad range of projects, but some of our proudest moments have come from critical use installations just like this — where the stakes are high, and the job requires perfect precision.
Our client, an aerospace general contractor, teamed with HPS for the installation of the tank storage area piping and the pad area piping for the launch pad. These stainless steel piping systems included rocket fuel piping, liquid oxygen (LO2) piping, liquid nitrogen (LN2) piping and gaseous helium (He) and nitrogen (N2) piping.
HPS was very excited about this on-site piping installation opportunity because part of the scope included the connection of fourteen stainless process piping control skids that were previously awarded to HPS in the months prior to the on-site project. These skids were welded and assembled at our fabrication facility in Manassas, VA. There’s nothing more satisfying than installing equipment that we built!
The Strategy
The site conditions for installation were quite challenging, to say the least – the project duration was 30 months, and it all happened on an island only a few yards away from the Atlantic Ocean. The constant wind, cold, heat, sand, mosquitoes, snowstorms, an earthquake, and even a hurricane all posed challenges! All this while tasked with producing 100% x-ray quality welds through NDT radiographic inspection and providing full NASA required documentation to support outer-orbit travel.
In addition to the challenging working conditions, due to the one-of-a-kind nature of this job, we had to be flexible in making engineering modifications throughout the entire project. Our team regularly met with the designers and NASA engineers to ensure that we were all on the same page about producing and installing the best product with the smallest amount of impact to the launch facility schedule.
All project materials were required to be purchased under the Buy American Act. Valves and components had long lead times, some up to 36 weeks, so proper planning and scheduling were a must.
HPS is always on the lookout for opportunities to improve the schedule while reducing costs. Mandrel bending the stainless piping, instead of welding, was an excellent way to accomplish this. By utilizing our mandrel bending equipment in our Manassas VA fabrication facility, we were able to remotely support the on-site installation and ensure that we weren’t impacted by the various site conditions we encountered at the launch pad.
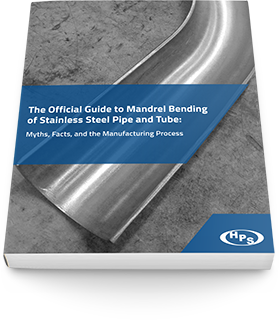
The official guide to mandrel bending
Separate facts from myths and save up to 50% on project costs compared to cutting and welding.
Our skilled team of project managers, welders and steamfitters collaborated to install various systems using a combination of TIG welded, and mandrel bent stainless steel piping from ½” through 12” ranging from schedule 10 to schedule XXH (Double Extra Heavy) wall thickness. Our team also flared tubing to connect AN 37 degree JIC fittings that were used in the control systems.
The on-site piping installation exceeded every specification for cleanliness and critical use required for this high stakes project. These standards included ASME B31.1, ASME B31.3 for severe cyclic conditions, NASA specifications and documentation, and IEST-STD-CC1246D cleanliness specifications. Expert TIG welders who had extensive training and experience performed the B31.3 severe cyclic welds.
The Result
By the end of the project, each system was a magnificent and complex network of stainless steel. We are proud that HPS’ on-site process piping installation was a critical part of this project.
Our careful execution helped NASA to reach for the stars and beyond with a successful rocket launch in February 2013!
Contact High Purity Systems
Have a question about a piping challenge? Want to discuss an upcoming project? Let’s talk.
Carbon Tower Upgrade
Comments Off on Carbon Tower UpgradeThe Challenge
Need milk? We can help. How about wine? We can help with that, too!
Recently, one of our customers needed water — and they needed it right away. The high-production purified water bottling company asked our High Purity Systems (HPS) team to replace a carbon tower at their facility.
The Strategy
Without affecting production, HPS replaced the carbon tower with a new model during a planned overnight shutdown from a Friday evening through Saturday morning. To combine multiple pieces to form the single carbon tower needed for this integral piece of equipment, we employed TIG welding, rigging, and tank assembly operations, as well as necessary in-service testing.
The customer chose High Purity Systems for the job thanks to our extensive team capabilities and our proximity to the customer’s Virginia location, which would surely help to expedite the project. We also had an existing relationship with the customer, who had been working with us since 2007 on a variety of facility challenges, including leaking equipment issues. Based on our past successful projects and consistent quality, the client trusted that we could deliver a timely solution for the carbon tower replacement project.
The Result
Our team replaced the carbon tower in less than 24 hours. After planning and executing a small facility shutdown, we assembled tank components using hand TIG welding and rigging equipment. Although outside the scope of our contract, we also installed the tank trimmings using polished stainless steel tube and fittings to meet food and beverage industry standards.
Once the tank was installed and facility operations were restored, the customer tested the carbon tower and said that, “Everything worked perfectly.” HPS provided a solution that would allow the facility to return to full operation without any extended downtime — and made for a very happy customer!
Contact High Purity Systems
Have a question about a piping challenge? Want to discuss an upcoming project? Let’s talk.
DI Water Drops
Comments Off on DI Water DropsThe Challenge
Johns Hopkins Bayview Medical Center has had a rich history in the Baltimore area since 1773. Ever since Johns Hopkins took over management in the 80s, Bayview Hospital has been a national leader in academic medicine. In 2012, the hospital decided to upgrade its critical Deionized (DI) water system. High Purity Systems had the privilege of working on this project to help get their critical system back online.
Over the years, High Purity Systems has built a strong working relationship with a local designer of water systems. Whenever the designer needs piping for large-scale systems or smaller-scale projects, they call HPS, just as they did with this Bayview project.
The Strategy
Our HPS team began the planning process by confirming schedules, materials, and layout. There was a collaborative discussion between the Bayview team, the water system designer and the HPS team about the best material to use for the DI water piping system; LXT or polypropylene? After several meetings with our client and representatives from Bayview, it was determined the originally specified LXT pipe would not be the best solution to build the piping system. Instead, it was determined that socket weld heat fusion polypropylene would be the more efficient and sanitary solution. After our client and Bayview representatives both agreed with the new approach, our team began working on the project.
Over the scheduled project timeline of four weeks, HPS installed the DI water loop in the ceiling with the appropriate slope for proper drainability. Once we completed the overhead piping and the ceilings, we continued the work on the walls and floors. HPS connected the system to the purification equipment our client provided. When the polypropylene piping was finished, HPS performed hydrostatic pressure testing to ensure a strong and leak-free system.
The Result
Our client recommended HPS for this project because over the years HPS has repeatedly proven its ability to deliver quality, sanitary piping systems. HPS’ consistency in delivering sanitary piping systems on time with few complications is the reason for our strong partnerships with clients like these.
At HPS, we admire the work Johns Hopkins Bayview Medical Center does in the medical field; our team was honored to contribute to facility improvements that will now help the Center to better care for their patients. By turning the initial project vision into a reality, HPS made not just one, but two clients happy with the final result.
Contact High Purity Systems
Have a question about a piping challenge? Want to discuss an upcoming project? Let’s talk.
Process Gas Demo
Leave a CommentThe Challenge
Site managers face a number of challenges when maintenance work is being performed in their manufacturing facility — namely, ensuring that the regular schedule of the plant is not interrupted. A High Purity Systems (HPS) customer recently faced this when preparing to cap and remove the process gas and water services originating from the main supply lines located in the ceiling of their plant.
The customer, a global leader in government and defense contracting, needed a company that could remove the process gas piping competently, as cutting the wrong line or turning off an incorrect valve would have devastating effects on production. That’s why they turned to the HPS team and our three decades of hands-on field experience and industry expertise, and an outstanding safety record for demolishing piping systems.
The Strategy
Instead of simply picking the lowest bidding contractor, the customer selected HPS because of our extensive knowledge of their facility — and in the end, our proposal also turned out to be the most cost-effective solution. Not only did we cap and demo the lines as required, but we finished the project with no disruptions to production as our customer had originally anticipated.
According to the job specifications, the project called for a high purity nitrogen line to be capped using a silver solder brazing method. The HPS team was able to provide an alternate solution involving a copper ProPress tool, a faster and less expensive method than silver solder brazing. This method eliminated the need for hot work permits, soldering, a fire watch, testing and recertification.
The Result
The customer trusted HPS’ judgment and ability to work safely and efficiently while adhering to a time and materials contract. As a result, we were able to provide a superior solution that brought the project in under budget. In fact, they were so impressed with the final product, our 100% accuracy, and our ability to go above and beyond to benefit the project that they have kept our time and materials contract open for future work.
Contact us today to learn more about how High Purity Systems can earn your TRUST and put our 30 years of experience to work improving your projects.
Contact High Purity Systems
Have a question about a piping challenge? Want to discuss an upcoming project? Let’s talk.
MOCVD Piping
Comments Off on MOCVD PipingThe Challenge
High quality process piping is the foundation of any laboratory. When a client from the semiconductor industry wanted to build a research and development laboratory, they called on High Purity Systems (HPS) to make sure the job was done properly.
During HPS’ initial overview of the job, we noted that laboratory development would require connecting and installing process piping lines for installation of a Metalorganic Chemical Vapor Deposition (MOCVD) tool using highly specialized equipment. For HPS, this project was well within our comfort zone.
Before delving into the project details, we want to thank — yes, thank — one of our competitors for helping our customer recognize that HPS provides unmatched services expertise. Our competitor subcontracted its installation work, which led the customer to question the competitor’s experience in performing high purity gas line installations and the company’s commitment to getting the job done right. At HPS, we are proud to say we perform our own installations — without subcontractors — and deliver unrivaled quality.
The Strategy
Ready to work, we consulted with the customer to determine the exact specifications required to develop their laboratory. The customer did not yet have a specific plan for how to go about connecting and routing the piping, so HPS was happy to create a detailed layout for the installation.
This was not the only barrier HPS faced in this piping system project. The customer didn’t specify the construction materials, a crucial detail that could have completely slowed down project completion. To expedite the process, our team helped the customer select materials that would meet all of the project objectives. Ultimately, HPS recommended stainless steel tubing, PFA, and PVC to help lower material costs. The customer agreed to the proposed plan and the project began.
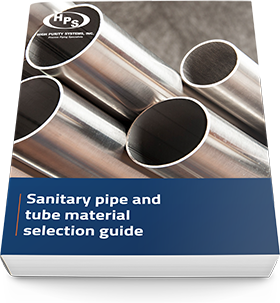
Sanitary pipe and tube material selection guide
See how matching materials to processes boosts performance and increases safety in your operations.
Our team installed process supply lines for liquid nitrogen, gaseous nitrogen, compressed dry air, ammonia, dilute silane, hydrogen, and a chilled water loop. All of these lines supported and connected the MOCVD tool, a Molecular Beam Epitaxy (MBE) system, silane, ammonia and nitrogen cabinets, a portable chiller, and the hydrogen bank that was located outside.
HPS used orbital welding equipment to install the single wall stainless steel tubing (Coaxial) for non-hazardous gases and double containment stainless steel tubing for highly combustible and hazardous gases. The tubing ranged from ¼” OD to ½” OD. Each line was pressure tested prior to completion. Once completed, our team had a third-party QA/QC validate the system’s analytical counts for turnover to the customer.
The Result
As with every job HPS tackles, our sincere dedication to quality and complete customer satisfaction on this project was unparalleled. Every weld was completed to American Society of Mechanical Engineers (ASME) B31.3 and semiconductor standards for weld oxidation limits and weld profile.
Once the project was complete, the customer was excited to use their finished laboratory. They appreciated High Purity Systems’ drive to deliver valuable guidance during project development, provide quick solutions to on-site challenges, and overcome unanticipated issues.
Contact High Purity Systems
Have a question about a piping challenge? Want to discuss an upcoming project? Let’s talk.
Vaporizer Piping
Leave a CommentThe Challenge
One of our long-time partners, a natural gas and propane provider to over a million residential, commercial, and industrial customers, recently called us to work on a new project. The customer reached out to High Purity Systems (HPS) to plan and execute the replacement of four propane vaporizers at its plant. A piping fabrication and installation project in which safety, schedule, and quality were of utmost importance.
Replacing the vaporizers (which were over 50 years old) with large piping spools, demanded a high degree of planning and precise fabrication with minimal margin of error. Over the course of the two month project, the customer asked our team to take measurements of the existing vaporizers, custom fabricate replacement piping to fit the old structure, and connect the four new vaporizers.
The Strategy
Before we could install the new vaporizers, our team needed to begin by removing the old ones. However, the only way in and out of the system was through the top of the steel structure that was built around the vaporizers; our team utilized an 80-ton crane and articulating lift to access the tops of the vaporizers 35 feet above ground level.
Because the piping was so old, there was also a high risk of shifting once HPS removed the existing units. The client trusted HPS’ experience to manage multiple large spools and make precise welds for a single assembly with minimal shifting.
Using RMD/MIG welding equipment, pipe positioners, and traditional stick welding equipment, HPS fabricated the spools, and then prior to installation, performed x-ray, magnaflux, and hydrostatic pressure testing to ensure standard compliance to ASME B31.3 standards.
Halfway through the installation, our on-site team realized that two of the new vaporizers had been manufactured differently, and this created issues that prevented a proper fit. The team quickly identified the discrepancy, brought it to our customer’s attention, and worked with the owner to resolve the problem. From start to finish, the customer was appreciative of HPS’ proactive communication throughout the project.
The Result
Prior to this project, HPS had a long history of collaboration with our client and built a reputation of safety, reliability, and high quality work. Our client’s project manager mentioned that when working with HPS, their teams never have to worry about oversight or the need to micromanage; the HPS team takes a high degree of accountability for every project, allowing customers to focus on other priorities.
Contact High Purity Systems
Have a question about a piping challenge? Want to discuss an upcoming project? Let’s talk.
Custom Digester Wiper
Comments Off on Custom Digester WiperThe Challenge
During a stainless steel support installation at a Virginia waste water treatment plant, the High Purity Systems (HPS) team overheard plant employees discussing a challenge. While trying to view the digester tank’s sludge level, an obstruction was affecting their ability to properly gauge the reduction of waste in the vessel and the rate at which new material could be added for processing.
The Strategy
The HPS team always loves a good challenge. The plant employees wanted a way to view the sludge level but knew they wouldn’t be able to keep any viewing port clear of the foam inside the tank. Being naturally curious, our team couldn’t resist investigating the manway at the top of the vessel, where a solid steel blind flange was installed.
After discussing potential options for a view port and various techniques to keep the manway view port clear, our team sketched out a wiper mechanism concept and explained the functionality to the waste water processing manager. After reviewing our initial concept our customer added the following requirements:
- Test to 5psi
- Use flame retardant material for all flanges, gaskets, and O-rings
- Connect to a non-standard flange
Even with these additional requirements, the HPS team was eager to develop a solution for the plant. Likewise, the team at the plant was so excited about potentially fixing the problem that they asked us to pursue a solution. The resulting proposition was a completely customized project. In fact, every single part of the wiper was custom-made for this application.
The HPS R&D team worked tirelessly to test possible configurations in both simulated CAD and prototype samples. Once the prototype was operating as we had envisioned, our team manufactured and installed it at the waste water treatment plant.
The Result
The customer loved the final product so much that employees frequently show it off to visitors touring the facility. At their urging, we are offering this product to other waste water treatment facilities experiencing the same challenge.
Contact High Purity Systems
Have a question about a piping challenge? Want to discuss an upcoming project? Let’s talk.
Silane Component Replacement
Leave a CommentThe Challenge
At HPS, we’re proud to be able to step into emergency situations for our customers as needed, providing quick, efficient service to remedy even the most complex issues. Recently, a large semiconductor company called us midday on a Friday after an argon issue dusted a silane (SiH4) piping line.
This dusting effect, which occurs when silane is exposed to a reactive gas or air, was the result of an improper cycle purge. Because silane is a highly flammable pyrophoric gas, it can undergo spontaneous combustion — which creates silica that then contaminates the piping system — without any external ignition.
The Strategy
Our team first needed to assess the damage; as soon as the internal piping is exposed to the atmosphere for cylinder changeout or maintenance, dusting of the internal piping will occur anywhere there is still any trace of silane present. This will typically determine how much of a system needs to be replaced — whether it’s a small section of piping or the entire system, including valve manifold panels and valve pigtails in the gas boxes.
Thankfully, the purging of the system was almost complete and this was only a minor combustion; there was no major explosion, no property damage aside from the piping, and no worker injuries. Mere hours before quitting time on Friday, HPS assembled a workforce to custom fabricate replacement piping over the weekend to help get our customer’s facility back up and running for the following week.
For this job, we needed to make over 200 ultra-high-purity orbital welds in our class 100 cleanroom to replace 18 individual sections (40 feet total) of damaged ¼-inch tubing. We were given the existing damaged lines with VCR caps to close them off, which allowed us to take accurate measurements for the replacement piping lines.
Luckily, we already had 316L stainless steel tubing, fittings, and VCR end connections in stock. Using automatic GTAW orbital welding, we were able to supply all 18 duplicated lines on Sunday evening so the customer could immediately begin reinstallation.
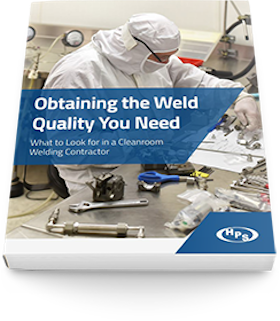
Obtaining the weld quality you need
Learn about the skills and resources necessary for successful cleanroom welding.
The Result
Our dedicated team worked all throughout Saturday and Sunday to complete the project before the start of the week, finishing the job in just two days. We also held our fabrication to tolerances of 0.020 inches and met the required SEMI welding standards. The customer was extremely grateful that we were able to tackle this issue so quickly and produce the reliable, high-quality piping needed for the emergency replacement.
To learn more about this job or how HPS has helped other customers solve problems at the eleventh hour, contact us today.
Contact High Purity Systems
Have a question about a piping challenge? Want to discuss an upcoming project? Let’s talk.
Condensate Valve Installation
Leave a CommentThe Challenge
Recently, an industry-leading biologics R&D organization asked the HPS team to put our versatile piping system expertise to work on a new project. The client needed to add shutoff valves to an existing condensate steam line in their life science facility, and our team was excited to take on the challenge.
The project involved welding valves onto three separate Water for Injection (WFI) generation skids. To orchestrate the valve installation, our team coordinated with the owner’s facility staff to ensure minimal down time for each of the three independent skids. However, we quickly had to become flexible about the job schedule when unexpected shutdown changes altered our plan.
The Strategy
While the facility owners originally planned for two separate shutdowns on the same day, they ended up being unable to bring the first piece of equipment back online in time to shut down the second piece; once the WFI skid was put into idle mode, the owner determined it could not be brought back online as quickly as expected. This unanticipated schedule change altered our team’s approach to the project, as both HPS and the owner had initially planned to complete two valve tie-ins within the first day.
At HPS, we always go out of our way to provide the services each customer needs to their exact specifications. We knew the importance of rescheduling the second shutdown and we were able to accommodate the customer by returning another day to complete the second and third valve installations. When we returned, our on-site team hand-welded the carbon steel valves and performed an in-service inspection test upon completion.
The Result
Despite the scheduling setback, HPS completed this project in just two days total, minimizing the owner’s operational downtime as well as their overall project costs. The customer appreciated our flexibility with the changing schedule and was very pleased with the final results of the project.
Contact High Purity Systems
Have a question about a piping challenge? Want to discuss an upcoming project? Let’s talk.
Purge Suitcase Panel
Leave a CommentThe Challenge
When customers approach custom fabrication companies with an idea or general scope of a job but with no prints or proposed project routes, the prototyping process can be challenging. To add to the complexity, these jobs often come with comprehensive lists of requirements. At High Purity Systems (HPS), we view these projects as opportunities to display our versatility and creativity, developing solutions that exceed even the customer’s original ideas.
Recently, for instance, NASA needed help developing a ground support gas delivery system that required strict contamination control during nitrogen purging applications. This project presented several challenges. In addition to requiring a clean panel, the purging would often be done in remote locations, such as the desert. Also, the completed purge suitcases needed to weigh less than 35 pounds each so that operators could manually carry them in compliance with government guidelines.
Aware of our previous aerospace orbital welding experience, NASA turned to us for help with these launch pad purification panels. After a 30-minute phone call with the client, we reviewed the two-page list of specifications and immediately set to work. No design, no layout, no problem.
The Strategy
Using only a supplied Piping and Instrumentation Diagram (P&ID) and a customer “wish list” of deliverables, we created a 3D model of the panel. Our preliminary conceptual prototype weighed 55 pounds, meaning the operator would need a lifting device to carry the panel. We evaluated the overall model and explored alternatives, ultimately deciding to use lighter materials and replace some bulky fittings with tube bends. The final remote gas purification panel weighed just 33 pounds.
After supplying NASA with the CAD layout and specs of our final concept, they gave us the green light to fabricate a prototype. Using orbital welding equipment and hand tube benders in our Class 100 Cleanroom, we fabricated a UHP (ultra-high purity) purification panel from stainless steel 316L that exceeded ASME standards, SEMI standards, and the customer’s final purification requirements.
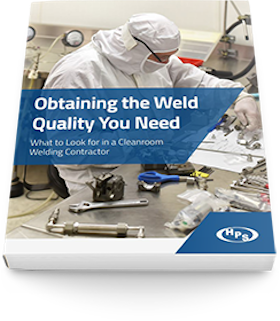
Obtaining the weld quality you need
Learn about the skills and resources necessary for successful cleanroom welding.
The Result
NASA was ecstatic with our final product and put in an order for 18 more lightweight purge suitcase panels — some to the exact initial prototype and others with variances in flow rates, pressure requirements, and number of outlets.
Creating a first-of-its-kind prototype, the skilled aerospace orbital welding team at HPS was able to turn a customer’s idea into a reality, with the final portable instrument gas purification panel exceeding all expectations. Since this project, NASA has remained a long-term partner and advocate for us, continuing to pass our name onto organizations with similar needs.
To discuss your next project or learn more about our past work — whether involving satellite purification projects or unique requirements — contact us today.
Contact High Purity Systems
Have a question about a piping challenge? Want to discuss an upcoming project? Let’s talk.