The Challenge
At HPS, we’re proud to be able to step into emergency situations for our customers as needed, providing quick, efficient service to remedy even the most complex issues. Recently, a large semiconductor company called us midday on a Friday after an argon issue dusted a silane (SiH4) piping line.
This dusting effect, which occurs when silane is exposed to a reactive gas or air, was the result of an improper cycle purge. Because silane is a highly flammable pyrophoric gas, it can undergo spontaneous combustion — which creates silica that then contaminates the piping system — without any external ignition.
The Strategy
Our team first needed to assess the damage; as soon as the internal piping is exposed to the atmosphere for cylinder changeout or maintenance, dusting of the internal piping will occur anywhere there is still any trace of silane present. This will typically determine how much of a system needs to be replaced — whether it’s a small section of piping or the entire system, including valve manifold panels and valve pigtails in the gas boxes.
Thankfully, the purging of the system was almost complete and this was only a minor combustion; there was no major explosion, no property damage aside from the piping, and no worker injuries. Mere hours before quitting time on Friday, HPS assembled a workforce to custom fabricate replacement piping over the weekend to help get our customer’s facility back up and running for the following week.
For this job, we needed to make over 200 ultra-high-purity orbital welds in our class 100 cleanroom to replace 18 individual sections (40 feet total) of damaged ¼-inch tubing. We were given the existing damaged lines with VCR caps to close them off, which allowed us to take accurate measurements for the replacement piping lines.
Luckily, we already had 316L stainless steel tubing, fittings, and VCR end connections in stock. Using automatic GTAW orbital welding, we were able to supply all 18 duplicated lines on Sunday evening so the customer could immediately begin reinstallation.
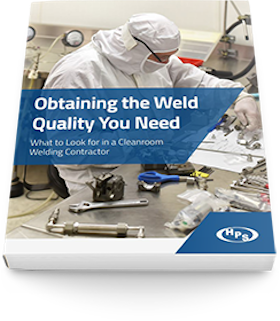
Obtaining the weld quality you need
Learn about the skills and resources necessary for successful cleanroom welding.
The Result
Our dedicated team worked all throughout Saturday and Sunday to complete the project before the start of the week, finishing the job in just two days. We also held our fabrication to tolerances of 0.020 inches and met the required SEMI welding standards. The customer was extremely grateful that we were able to tackle this issue so quickly and produce the reliable, high-quality piping needed for the emergency replacement.
To learn more about this job or how HPS has helped other customers solve problems at the eleventh hour, contact us today.
Contact High Purity Systems
Have a question about a piping challenge? Want to discuss an upcoming project? Let’s talk.