The Challenge
When customers approach custom fabrication companies with an idea or general scope of a job but with no prints or proposed project routes, the prototyping process can be challenging. To add to the complexity, these jobs often come with comprehensive lists of requirements. At High Purity Systems (HPS), we view these projects as opportunities to display our versatility and creativity, developing solutions that exceed even the customer’s original ideas.
Recently, for instance, NASA needed help developing a ground support gas delivery system that required strict contamination control during nitrogen purging applications. This project presented several challenges. In addition to requiring a clean panel, the purging would often be done in remote locations, such as the desert. Also, the completed purge suitcases needed to weigh less than 35 pounds each so that operators could manually carry them in compliance with government guidelines.
Aware of our previous aerospace orbital welding experience, NASA turned to us for help with these launch pad purification panels. After a 30-minute phone call with the client, we reviewed the two-page list of specifications and immediately set to work. No design, no layout, no problem.
The Strategy
Using only a supplied Piping and Instrumentation Diagram (P&ID) and a customer “wish list” of deliverables, we created a 3D model of the panel. Our preliminary conceptual prototype weighed 55 pounds, meaning the operator would need a lifting device to carry the panel. We evaluated the overall model and explored alternatives, ultimately deciding to use lighter materials and replace some bulky fittings with tube bends. The final remote gas purification panel weighed just 33 pounds.
After supplying NASA with the CAD layout and specs of our final concept, they gave us the green light to fabricate a prototype. Using orbital welding equipment and hand tube benders in our Class 100 Cleanroom, we fabricated a UHP (ultra-high purity) purification panel from stainless steel 316L that exceeded ASME standards, SEMI standards, and the customer’s final purification requirements.
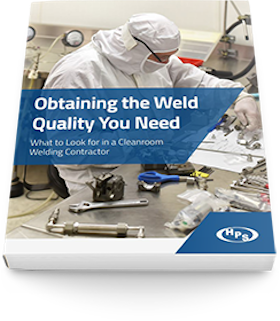
Obtaining the weld quality you need
Learn about the skills and resources necessary for successful cleanroom welding.
The Result
NASA was ecstatic with our final product and put in an order for 18 more lightweight purge suitcase panels — some to the exact initial prototype and others with variances in flow rates, pressure requirements, and number of outlets.
Creating a first-of-its-kind prototype, the skilled aerospace orbital welding team at HPS was able to turn a customer’s idea into a reality, with the final portable instrument gas purification panel exceeding all expectations. Since this project, NASA has remained a long-term partner and advocate for us, continuing to pass our name onto organizations with similar needs.
To discuss your next project or learn more about our past work — whether involving satellite purification projects or unique requirements — contact us today.
Contact High Purity Systems
Have a question about a piping challenge? Want to discuss an upcoming project? Let’s talk.