The Challenge
High Purity Systems (HPS) is a clean piping system installation and fabrication service provider for the semiconductor, aerospace, and bio-pharmaceutical industries, and our team recently showcased its diverse capabilities when a large microelectronics company approached our staff for help.
The customer — a global fiber optics, motion control, light analysis, and optomechanics product manufacturer — needed to relocate its existing ammonia (NH3) and silane (SiH4) gas cabinets and the associated ductwork and piping. They turned to our team, with years of experience in field service and project management experience, to guide this multi-step gas system installation project from start to finish.
The Strategy
We differentiate ourselves by having a thorough understanding of our customer’s specific facility protocols, as well as the client’s end goals and project deadline. Our on-site team knew the right questions to ask to better understand the client’s daily operations and adapt our work process to fit their needs accordingly.
Upon having a clear understanding of the customer’s work environment, we disconnected the existing gas cabinets and removed the ductwork and associated piping. We then relocated the cabinets to the desired location and added new silane, ammonia, compressed air, nitrogen, and oxygen lines, as well as ductwork for the exhaust.
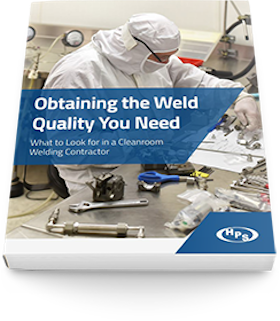
Obtaining the weld quality you need
Learn about the skills and resources necessary for successful cleanroom welding.
Using an orbital welding process, our team installed 316L stainless steel ammonia and silane lines with coaxial tubing to create a double contained system. VCR and compression fittings secured the 15Ra, 1/4″ x 1/2” coaxial gas lines.
Upon completion of the installation, a pressure test was performed on both the inner 1/4” process line and the outer 1/2” containment line, as well as analytical testing to confirm purity. The finished product, which met the international SEMI standards for cleanroom safety and cleanliness, was turned over to the customer in three weeks.
The Result
This multi-step gas cabinet relocation and installation demonstrated that in addition to our work in smaller research and development labs, HPS also executes projects in larger semiconductor manufacturing plants. This project demanded HPS’ expertise with ultra-high purity cleanroom piping systems as well as double containment coaxial systems for hazardous materials.
The customer chose our team for our strong industry reputation and extensive resume, and we provided them with competitive pricing and flexible start and completion dates to meet their manufacturing schedule.
Think we can work together to solve a similar problem in your facility? Contact us now.
Contact High Purity Systems
Have a question about a piping challenge? Want to discuss an upcoming project? Let’s talk.