To ensure precise, high-quality orbital welds, it’s imperative to work with a cleanroom welding contractor that thoroughly trains its team. All too often, inexperienced technicians end up being told they are welders and acting merely as button pushers, unable to make real-time adjustments to programs or notice subtle inconsistencies in welds. If left unaddressed, these weld issues can lead to production impacts for the end user, which can affect costs and schedules.
The Importance of Training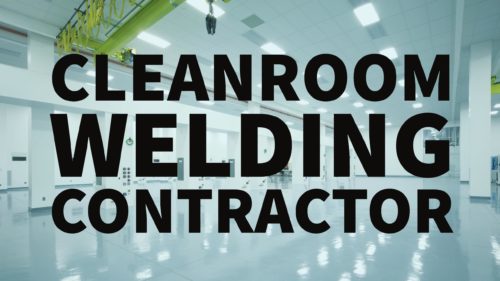
A skilled welder with the proper training, on the other hand, is indispensable to the process of creating consistent quality welds. Highly esteemed masters of their craft, they have spent years honing it to perfection. They are capable of creating their own welding programs and can make modifications immediately if they notice an issue, giving them a greater sense of ownership and pride in their work, which directly correlates to weld quality.
When a contractor provides its welders with the expected weld parameters, the team develops a thorough understanding of what a quality precision weld should look like and why — down to the tiniest details that may not be immediately apparent. Not only do they have the eye to identify inconsistencies early on, but they can also make necessary adjustments to eliminate unforeseen issues that would eventually affect the QA process and strict standards compliance.
Why Process Matters
Every welding shop has a set of processes and equipment, and a good shop will train each employee on these specific tools and capabilities — from weld heads to power supply fixtures — as well as how to adjust the welding parameters on each machine. Ultra-High Purity (UHP) welding, especially, requires extensive training on proper cleanroom procedures, as the slightest breach of protocol could contaminate the weld and require the weld to be cut out. A high purity weld is as much about the purging as it is about the welding process itself. A button pusher rarely understands the intricacies of purge pressure and required flows to make a UHP weld.
The HPS Team
High Purity Systems is proud to employ an experienced team of welders, each of whom has completed a five-year in-house apprenticeship-to-journeyman program to perfect their craft. During this time, each welder becomes familiar with all aspects of our systems and equipment, including specialized cleanroom protocol and our seven proprietary tools, such as the “Go/No Go” weld profile gauge and our back purge controller.
If you need assistance choosing the right cleanroom welding partner to team with to deliver high-quality, repeatable welds, download our free eBook, “Obtaining the Weld Quality You Need — What to Look for in a Cleanroom Welding Contractor.”
Contact High Purity Systems
Have a question about a piping challenge? Want to discuss an upcoming project? Let’s talk.