The Challenge
The ultra-high purity gas delivery systems in microelectronics facilities play a key role in the production of the sensitive components we rely on every day. But the parts that make up these important systems don’t last forever.
Our client, a major microelectronics component producer located on the East Coast, faced a dilemma: Inert regulator sticks inside ten of their valve manifold boxes were nearing the end of their service lives. Replacements were necessary. The customer had two options, and each was unattractive:
- Order replacement parts from the OEM who made the sticks in the first place. It would take the OEM 20 weeks to fulfill the order.
- Have entirely new valve manifold boxes built—an overly excessive and costly solution.
The customer approached High Purity Systems in search of a cost-effective alternative that wouldn’t result in months of downtime.
The Strategy
After carefully studying the customer’s drawings and specs for the regulator sticks, our team determined we could reverse-engineer them. Then, we would fabricate in a fraction of the time parts the OEM claimed wouldn’t be ready for almost five months.
Next, we ordered the materials. Because the part would be used in high purity microelectronic manufacturing, we ordered 316L stainless steel components. The elevated chromium content in 316L stainless steel offers improved corrosion resistance over other stainless steel formulas. The wetted surfaces of the components were electropolished to 10 Ra or better, further improving their corrosion resistance.
Then, we fabricated the parts. Due to the sensitive nature of the components, this was done in our in-house Class 100 cleanroom. Our skilled craftsmen used autogenous orbital welding equipment to perform welds meeting ASME B31.3 and SEMI standards.
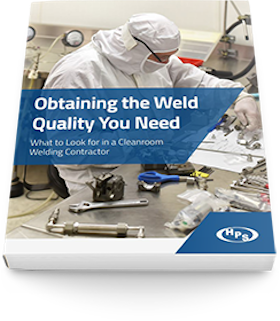
Obtaining the weld quality you need
Learn about the skills and resources necessary for successful cleanroom welding.
The result
We hand-delivered the regulator sticks to our customer’s plant just ten weeks after we took on the job, cutting in half the time the customer had to go without these critical parts had they engaged the OEM. Most of that time—eight weeks, to be exact—was spent waiting for raw materials with long lead times.
As a result of our quick work, our customer’s facility was back up and running much sooner than they anticipated. That directly translated to a lower project cost and more revenue earned.
High Purity Systems has excelled in understanding customers’ systems—including systems that someone else built. As a preferred alternative to OEMs, we go beyond fabricating replacement parts by helping customers develop their equipment maintenance programs.
Learn more about what to look for in a cleanroom welding contractor by reading our guide on the subject. Then, let’s talk about the difference our expertise can make in your facility.
Contact High Purity Systems
Have a question about a piping challenge? Want to discuss an upcoming project? Let’s talk.